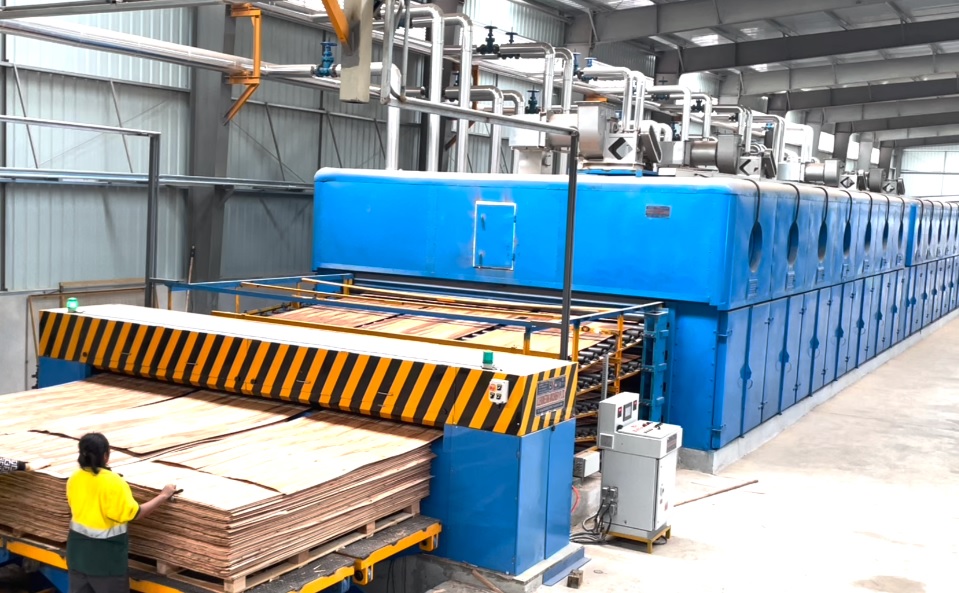
High humidity can pose challenges to the drying process of core veneer in the wood industry. Controlling the drying conditions becomes crucial to ensure the quality of the final product.
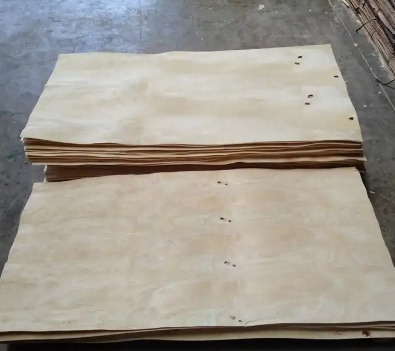
Here are some precautions that may be required when drying core veneer in high humidity conditions:
- Controlled Environment:
- Ensure that the drying area is well-enclosed and has proper insulation to minimize the impact of external humidity.
- Dehumidification:
- Consider using dehumidifiers to reduce the moisture content in the air. This can help create a more favorable environment for the drying process.
- Ventilation:
- Good ventilation is essential. Adequate airflow helps carry away moisture from the drying area. Use fans strategically to promote air circulation.
- Temperature Control:
- Maintain a controlled temperature. Higher temperatures can help accelerate the drying process. However, it’s important to strike a balance to prevent over-drying or other quality issues.
- Monitoring Moisture Content:
- Regularly monitor the moisture content of the core veneer at different stages of drying. This helps prevent under-drying or over-drying, both of which can affect the quality of the final product.
- Adjust Drying Time:
- Be flexible with the drying time. Depending on the humidity levels, it might be necessary to extend the drying time to achieve the desired moisture content.
- Stacking and Spacing:
- Arrange the veneer properly on drying racks to allow for optimal air circulation. Avoid overcrowding, as this can impede the drying process.
- Prevent Mold and Fungi:
- High humidity can lead to the growth of mold and fungi. Apply appropriate fungicides to prevent microbial infestation.
- Quality Checks:
- Conduct regular quality checks on the core veneer during the drying process. Address any issues promptly to ensure that the final product meets quality standards.
- Documentation and Record Keeping:
- Keep detailed records of the drying process, including environmental conditions, drying times, and any adjustments made. This information can be valuable for troubleshooting and process optimization.
It’s important to note that the specific precautions may vary depending on the type of wood, the drying equipment used, and the overall production setup. Regularly assess and adjust the drying process based on environmental conditions to achieve consistent and high-quality results.